Since 2021, a growing team of experts have been working away building, designing and fine-tuning everything from solar integration projects to exhibition stands just a stone’s throw from Sono HQ. At CES in the same year, we presented our solar trailer to showcase our Sono Solar team’s continued work towards making every vehicle solar and to kick-start collaborative B2B projects and testing with a wide range of companies from the transportation sector.
To make progress on this, we needed to put our expertise and energy full force into testing and improving our solar technology. In order to do this we set up a team with diverse skill sets to work alongside our engineers. The space we find ourselves in, in today’s interview, was where this all took place. We spoke to workshop supervisor Johannes, to answer all our questions about the capacious work space where all the magic happens.
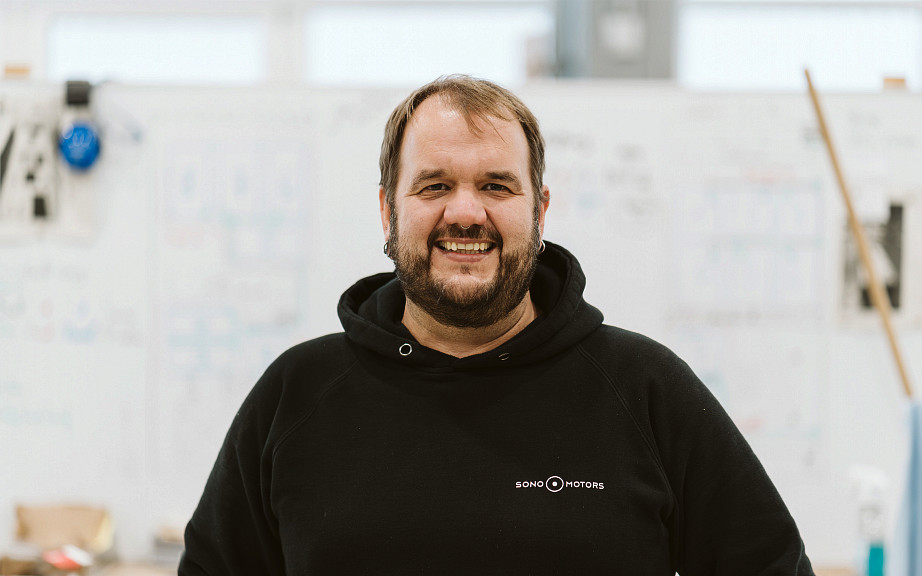
Lucy: Hi Johannes, thanks for taking the time out to talk a bit about all things workshop. Could you give our readers a brief introduction of yourself?
Johannes: Hello Lucy, thanks for coming to see us over here. Yes of course: my name is Johannes. I am the workshop supervisor and a trained automotive mechanic. I’ve had the classic career in my field, you could say, having worked in various roles at various automotive companies refining my skills, as well as as a paramedic. So, when I looked to change, I searched for vacancies in companies where I could feel pride in my work and see it making a difference.
I came across Sono Motors and was really taken by their mission and spirit, and realized that it would be a perfect fit for me. Luckily, Sono felt the same from their side. I joined in 2019 and was basically doing all the jobs that you now see our growing team doing. I was an electrician, automotive mechanic, assembler, constructor all in one.
Lucy: Thanks Johannes, that’s quite a story. When you walk into the workshop you clearly see that there's a lot going on. What exactly happens here?
Johannes: Well, this space is used predominantly for Sono Solar partnership projects and prototype manufacturing. This is where we work on everything that Sono is involved in terms of engineering, homologation, manufacturing, material science, photovoltaic technology, and electrical & mechanical integration. We carry out testing and procedural tasks on all vehicles that come through Sono, be it the Sion or something for a B2B solar customer like buses, trucks, trailers, e-vans and RVs. It all comes through us. We also work in close collaboration with our engineering team every single day. They also have their offices here, so we can all be right in the thick of it together.
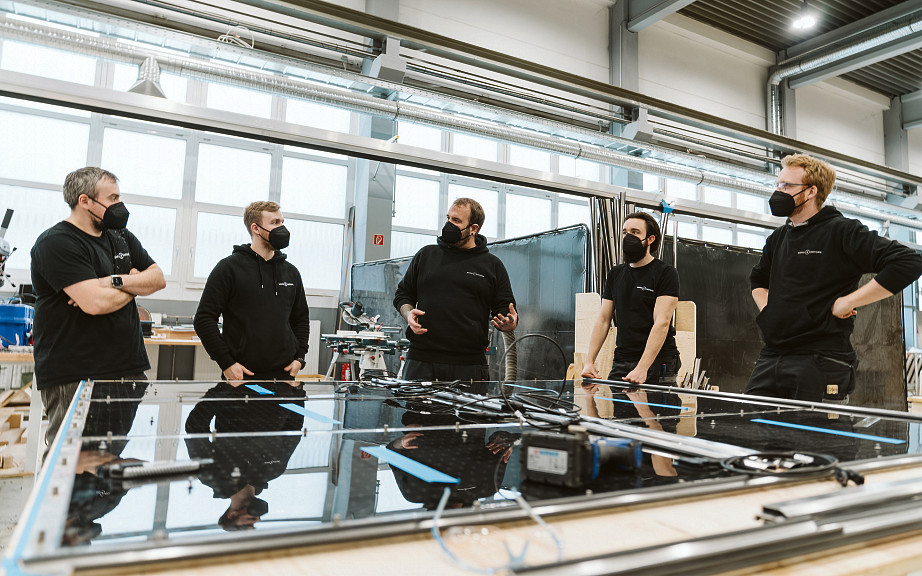
This workshop is where most of the physical testing is done, as we need to make sure that what has been designed and engineered by our development team is actually possible in reality. We also work on any construction projects that are needed by the company as a whole, like stand building for exhibitions or tours and, if we have time, we help out with tasks needed at the office itself.
Lucy: Oh wow, that’s pretty diverse. This space seems perfect for this and your team, it’s so close to Sono HQ too. How did this come about, because this is a fairly recent acquisition isn’t it?
Johannes: Well, it’s an interesting story really. When I started in 2019 it was just me in a room smaller than the one we’re in now [author’s note: we’re sat in the 30 sqm upstairs office in the workshop, for readers at home] doing everything that we as a team now do. Both the team and our space have, thankfully, since grown, and we remained there until last year, when we got wind that the workshop just across the road from our HQ used by a top automotive supplier was up for rent.
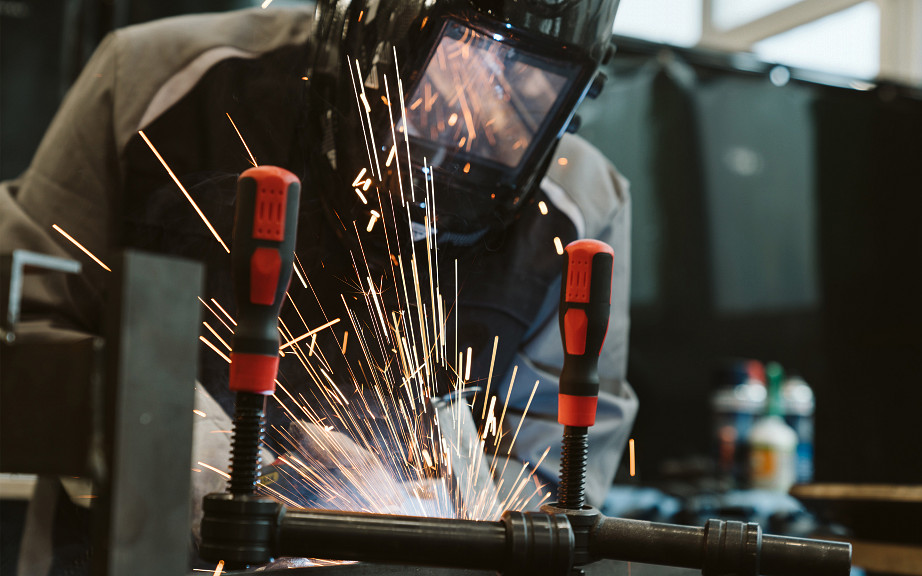
When we moved in we gutted it quite extensively so we would be able to bring large vehicles and equipment in if we needed. It’s really transformed our work and output capacity and we’ve already managed to pack it with the multitude of projects that we’re working on.
Lucy: That’s a huge difference and really every time I come here there’s always something new or different going on. The two Sion prototypes we currently have here are often in our workshop for development but also a huge range of different vehicles that are linked to our solar B2B collaborations. Can you tell us about one of those and how the process looked?
Johannes: Well, we’ve worked on a lot of different vehicles like buses, trailers, and last-mile vehicles. One of our latest projects involved integrating our solar technology into the cargo box of such a prototype vehicle for ARI Motors to enable range extension, which was displayed at the Intersolar exhibition last year in Munich. Extending range is something that is a clear benefit for solar mobility as it reduces huge costs. For reference, a standard truck does around 1 million km in its life-cycle.
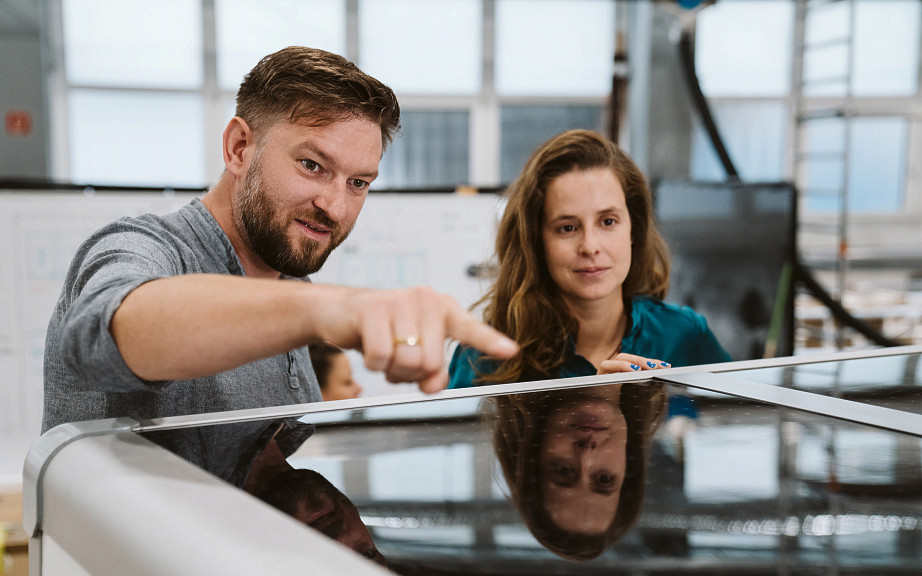
The integration process involved us being in very close contact with ARI Motors to ensure that we had a complete 360° view of everything that was involved in us integrating this technology. We worked with in-house development and engineering teams to plan how to accomplish this and made sure we inspected the vehicle itself so as to fully comprehend the specific parameters we were working with.
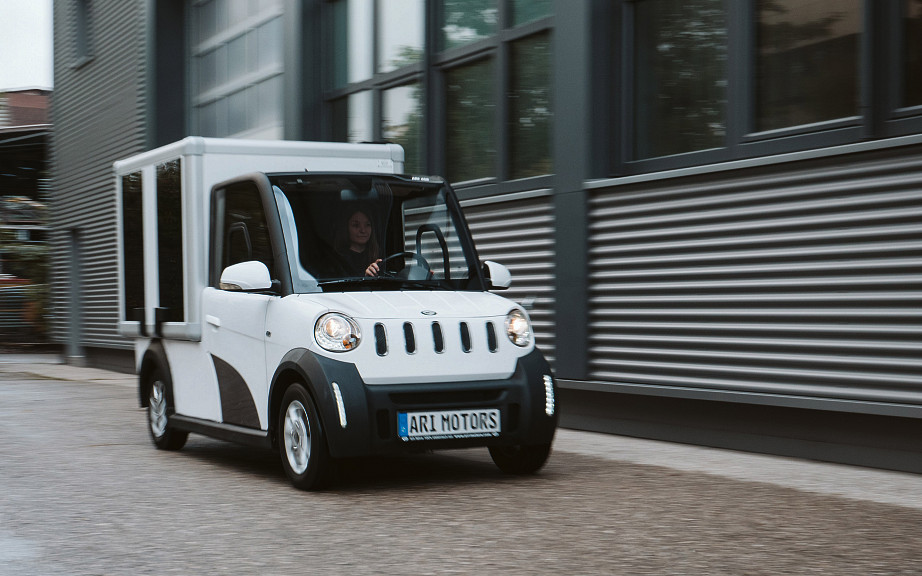
We have had so many different types of vehicles come to our workshop to undergo testing for a huge range of areas that come into play when integrating solar technology. These include the integration methods themselves, as well as heat testing, electrical integration and benchmarking different PV (photovoltaic) technology. This process again involves us working in collaboration with our development and engineering teams.
Lucy: So your team are involved from start to finish in all vehicle fittings. You get a wide variety of vehicles to fit, like that of ARI Motors, that must make it difficult to come up with a one size fits all approach.
Johannes: Yes, exactly. Every case is different. No two vehicles are the same. All vehicles are designed and specified differently according to their needs. For example on one vehicle the antenna could be at the back, but on another it’s at the front. One has extensive additional electronic systems that require extra power. The list goes on. That’s why when we came up with our procedure, we specified that we needed to be there right from the beginning.
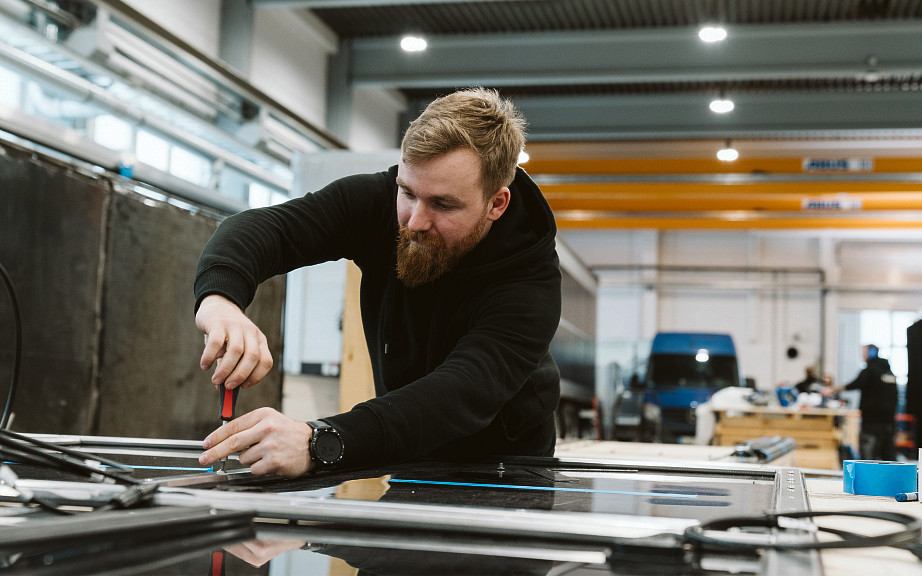
We need to examine where to position the PV panels. We need to know how our MPPT unit — the MCU — will be integrated into the existing vehicles’ electronics and how to connect them to the high or low-voltage vehicle battery, to name just a few. Basically, we tailor our installation methods based on the individual project. This type of process flexibility requires a hugely diverse set of skills, so I built the team accordingly. We need each individual member of our team to bring something different to the table so that we are covering all bases.
Lucy: Your team has come such a long way since you started in 2019. Could you tell me a little bit about its members?
Johannes: Yes, of course. So we have Kristijan, our electrician; Thomas who brings many years experience in model assembly and construction; Janek is a carpenter and has fantastic amounts of experience with solar technology, a real all-rounder. We then have Rouven who has extensive experience with the construction of expedition trucks and solar integration onto vehicles like camper vans. Jakob is our resident automotive mechanic and we recently brought Alexander in to support him, as their workload will be increasing considerably with the latest generation of prototypes as well as multiple B2B collaborations this coming year.
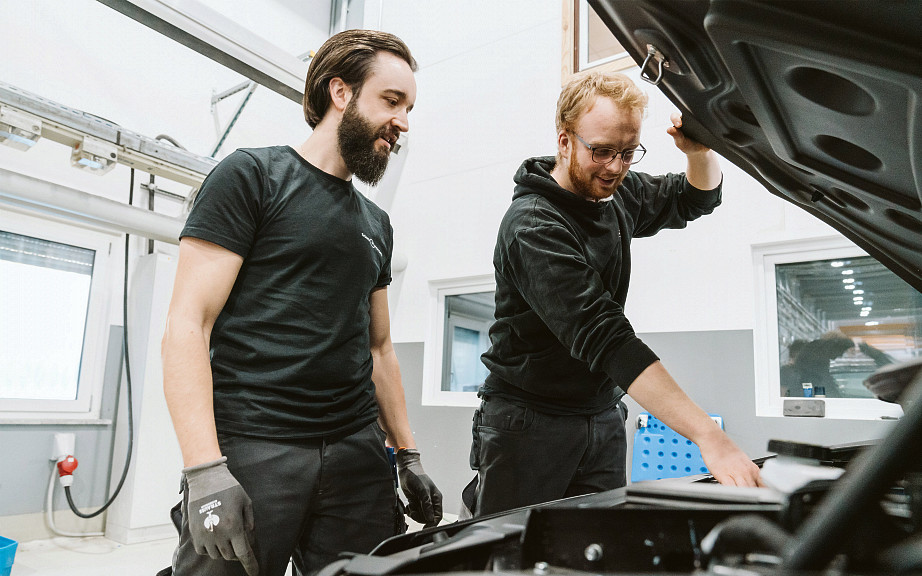
Lucy: I can really imagine you mean to go on as you started, so to speak. What are some of the big challenges facing the team in 2022?
Johannes: Well of course we want to continue to grow as a team and really expand our project catalog. As I said, we are in the process of establishing more collaborations, which will involve more travel, equipment and testing. It’s an exciting time and it brings a lot of opportunities for us.
Lucy: That sounds very promising. You’ve built a really solid team with very diverse skill sets. I imagine this is imperative for your work here but that it’s quite a task to find people who fit your needs as well as the culture you want to create here that reflects the company. Would you agree?
Johannes: Yes, absolutely. When I started building this team, it was very important to me that we define what skills we need to really optimize our work, but it was also really important to me that this team be like a family. We work so closely with one another and have to really trust each other because of the physical nature of our job but also working at Sono, we are like a family. Very supportive, very open and very passionate about why we do what we do. I’m so pleased with how our team has turned out and am excited to see where we will progress in the future.
Lucy: Is there any moment that springs to mind when you knew that Sono was right for you?
Johannes: Well there are a few that were really proud moments for me. I worked on the Crowdfunding campaign just a few months after starting which involved driving all across the country, to a different city every day, and doing buildup and break-down of all our stand equipment as well as any fixes to the vehicles we had back then. It was really great to experience how much people really believed in Sono Motors and its vision. It was really inspiring, but wow was it tiring. Very worth it with all we achieved and the support we received. That’s actually when I knew that Sono was somewhere I could really see myself and a company that I would be proud to work for.
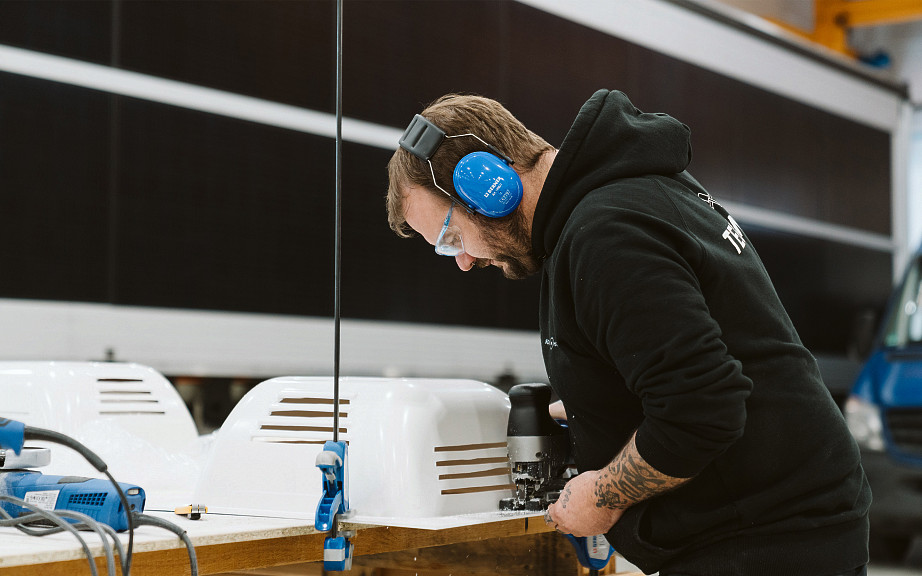
Lucy: It must be a really great feeling to see dreams become reality in a sense. How do you feel about what the future holds?
Johannes: What’s great for me is that no two days are the same. We are always working on really exciting and ground breaking projects that will enable mobility without the use of fossil fuels. As you can see, we’re leading the way and on the journey to our goal of solar on every vehicle.
Lucy: What a perfect note to end on. The work you do here is really important and mostly remains behind the scenes, so I’m really glad we were able to shine a light on it today. Thanks so much for taking the time, Johannes. Keep doing what you’re doing!