Whether we like it or not, in Germany, millions of people drive cars every day. According to a 2017 study by survey institute Infas, cars are by far the most popular means of transport. It is, therefore, not surprising that of the 3.2 billion kilometers covered every day in Germany, around 60 percent are covered by the help of our beloved automobile.
What exactly goes on in the vehicle while we are carefully maneuvering it through city congestion and along expressways throughout the country is of secondary importance – at least for those of us who are not automobile enthusiasts. And yet the chassis, and therefore also an automobile’s steering, is a key aspect, especially when it comes to the driving experience. A car with power steering and one without are worlds apart, for example.
Our partner for chassis: TRE
When selecting a suitable axle concept back in 2018, we got together with an expert from the world of motorsport – Team Rosberg Engineering, or TRE for short. The company based in Neustadt an der Weinstraße takes its name from Keke Rosberg, race car driver and Formula One world champion.
In the late 1990s, Rosberg adopted the approach of incorporating expertise from the world of motorsport into the development of production vehicles. His idea was to establish a development center for chassis systems which drew on the expertise of race engineers so that standard automobile manufacturers could benefit, too. TRE is now a leading light in the field of chassis development.
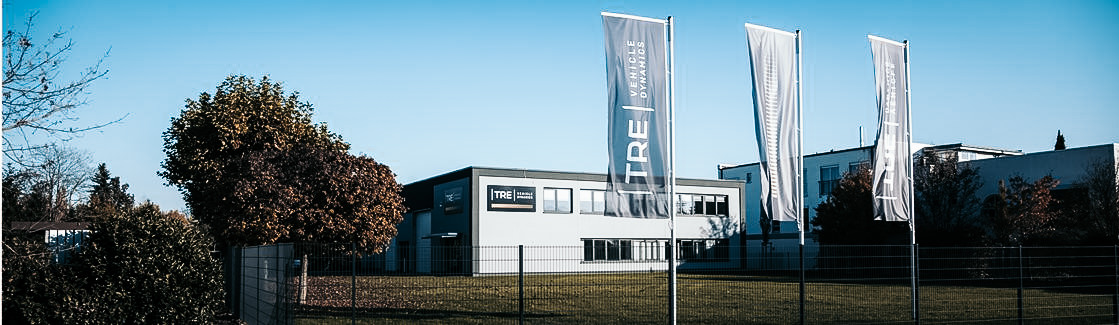
CEO Eckardt Döhrer describes the company’s vision as follows: “TRE has set itself the goal of serving its customers as a one-stop shop for every development step from the blank sheet of paper through to a prototype, if required. In our collaboration with Sono Motors, we are developing the entire suspension and chassis system for the production vehicle and prototype.”
Bringing Computer Models to the Streets
When developing vehicle parts, computer-based work is essential. Engineers design the various components and put them all together with the aid of CAD models. A great many factors have to be taken into account in the process. “At TRE, "the scope of work is divided into three areas: design, simulation, and production," explains Axel Hoffmann, Head of Chassis Development. “The Design team designs the chassis and the components on the basis of making the best possible use of the available space.”
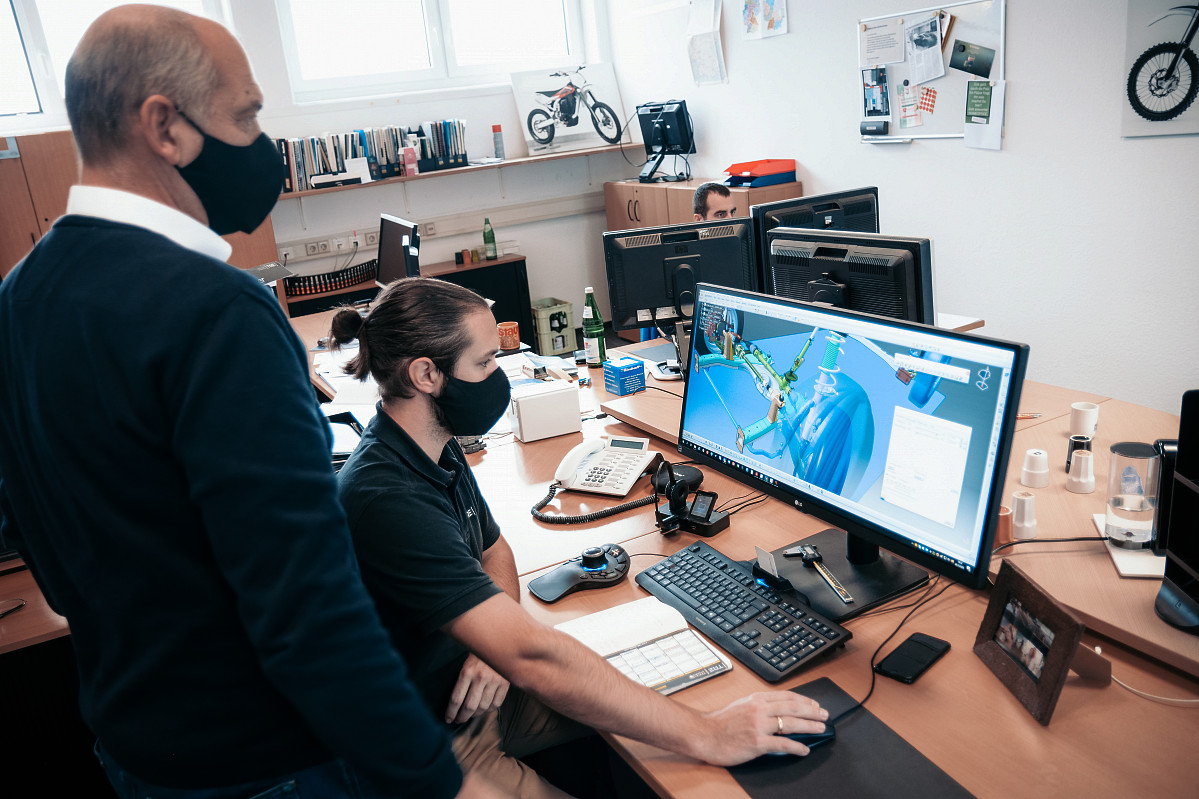
The development of what’s known as the subframe is especially interesting. The engineers developed it to provide high lateral stiffness and high deformability of the frame in case of a frontal collision. These two objectives must be reconciled with the particular space requirements of an electric drive.
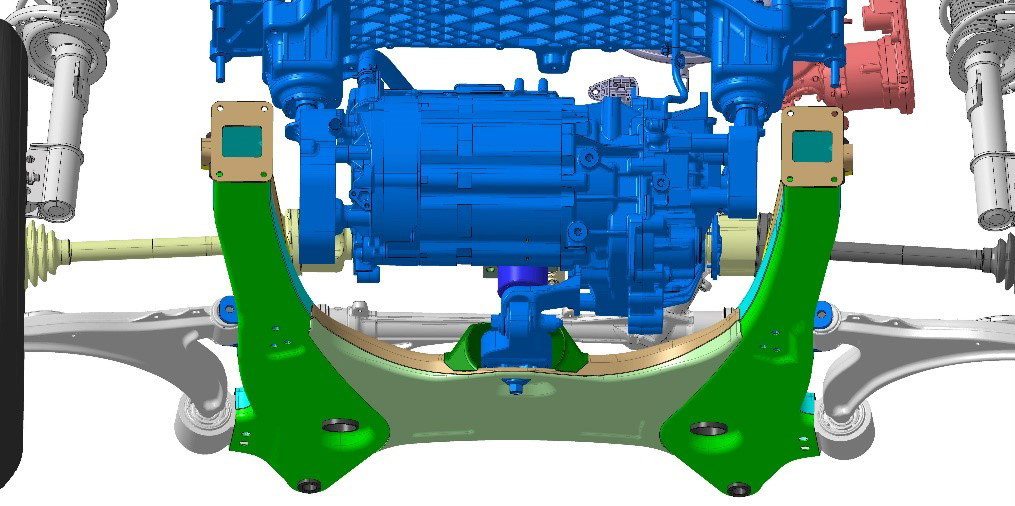
The positioning of all the chassis components is determined in close cooperation with the Multibody Simulation team. In the process, the developers also evaluate the kinematic characteristics and their influence on the construction.
TRE thoroughly analyzed the Sion’s steering system in particular, as the requirements regarding steering wheel position, pedal clearance, steering angle, and kinematics had to be met in a very tight space.
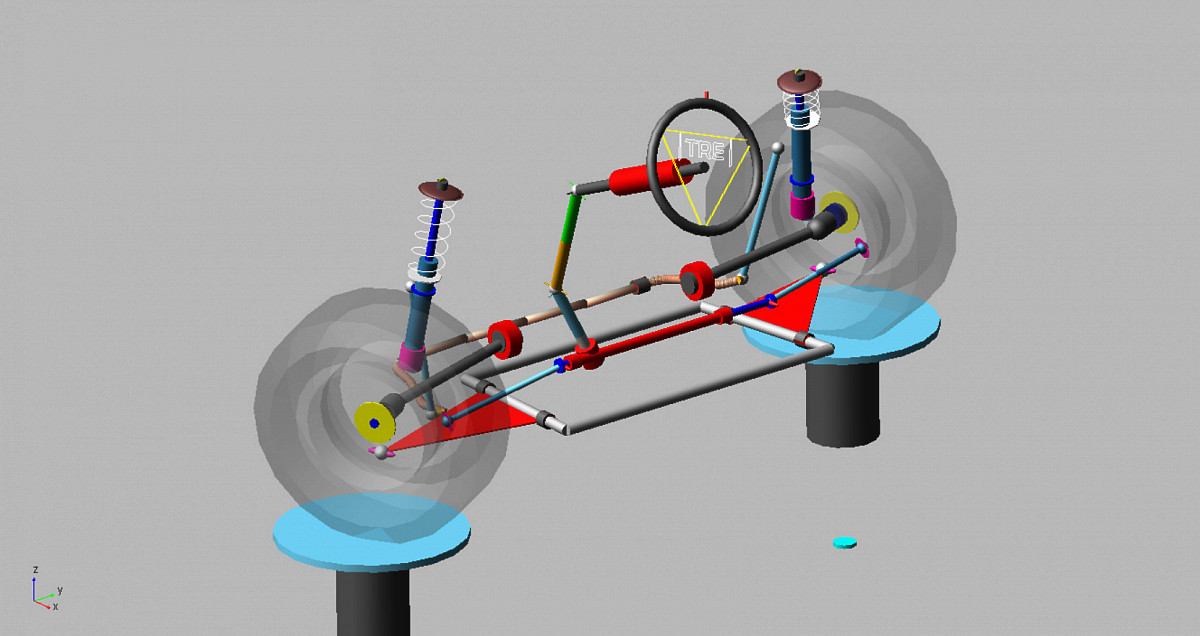
The components of potential suppliers are incorporated into the computer simulations at this stage, too, in order for the desired overall vehicle behavior to be achieved. This allows the engineers to incorporate the vehicle requirements – lateral, longitudinal, and vertical dynamics, comfort, sufficient ground clearance, a tight turning circle – into their calculations and take them into account.
The developers additionally simulate various load conditions, firstly to check the elastic flexibility and secondly to test the vehicle’s ground clearance. The results are presented to everyone involved as a CAD model.
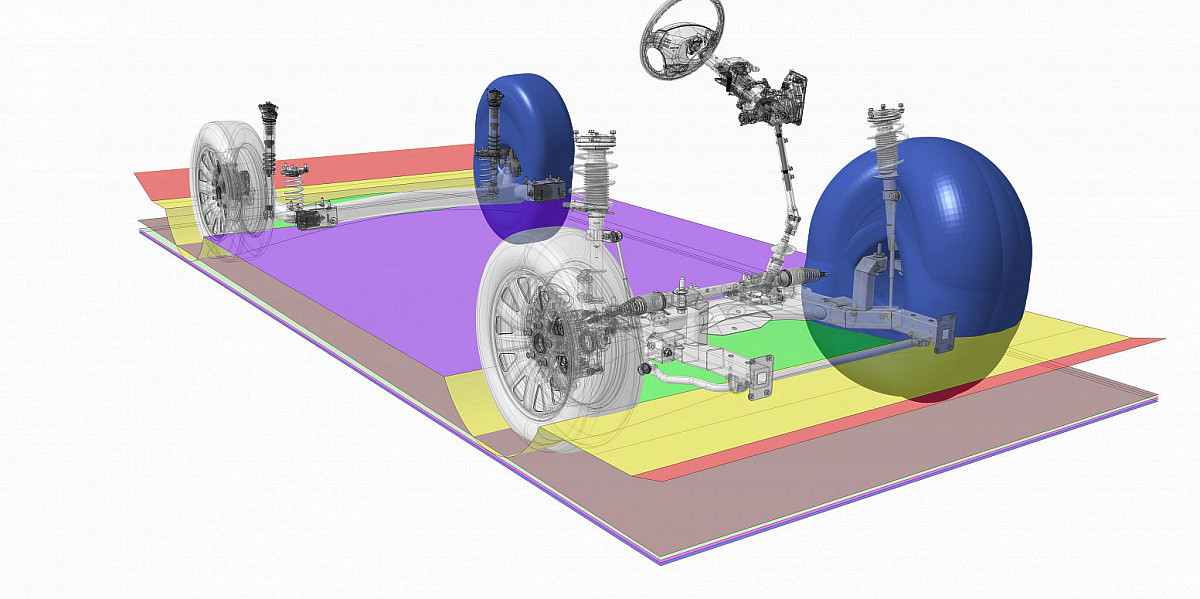
A number of parts had to be manufactured manually for the new prototype on the basis of the chassis developments for mass production. In June of this year, TRE began to derive the construction of the entire chassis for the prototypes from the status at that time of the CAD model for production vehicles.
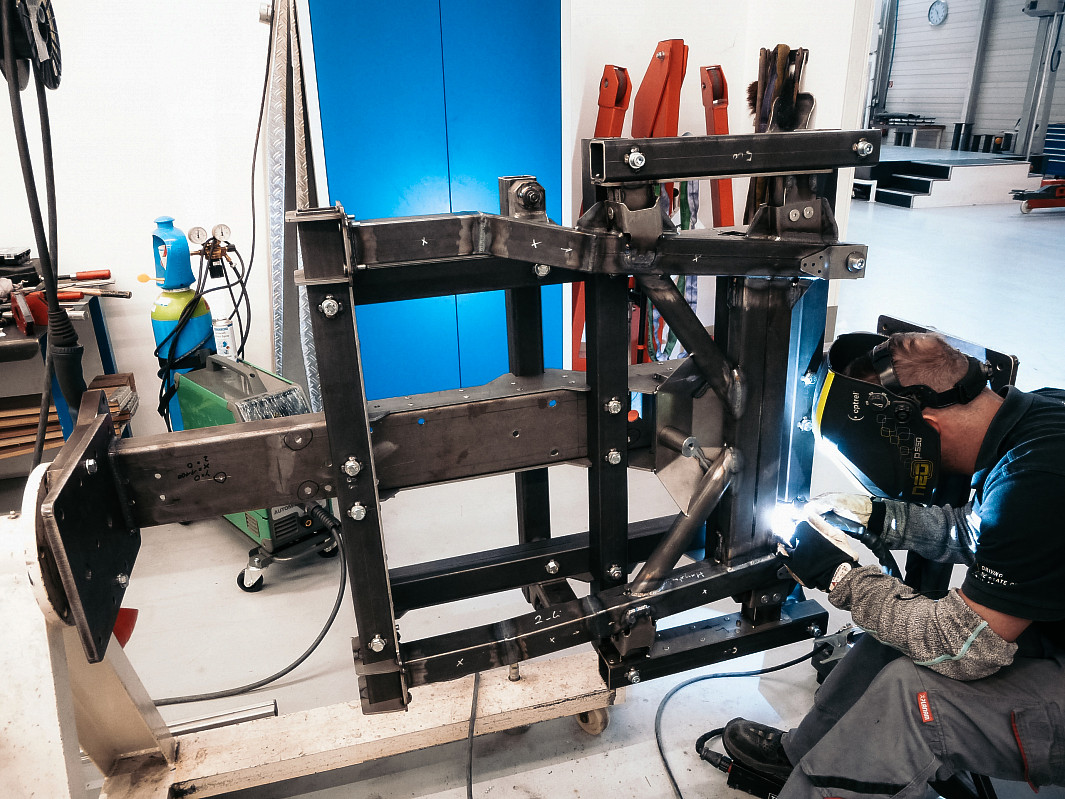
“For parts like the subframe, spindle, stabilizer bar, and twist beam which are manufactured in large numbers for mass production using costly tools, we designed more efficient, prototype-based manufacturing processes,” explains Axel Hoffmann. “The prototype parts constructed in this way boast properties and functions which already largely match those in a production vehicle in spite of series tools not being used. This means the vehicles can be used for tuning drives and road tests.”
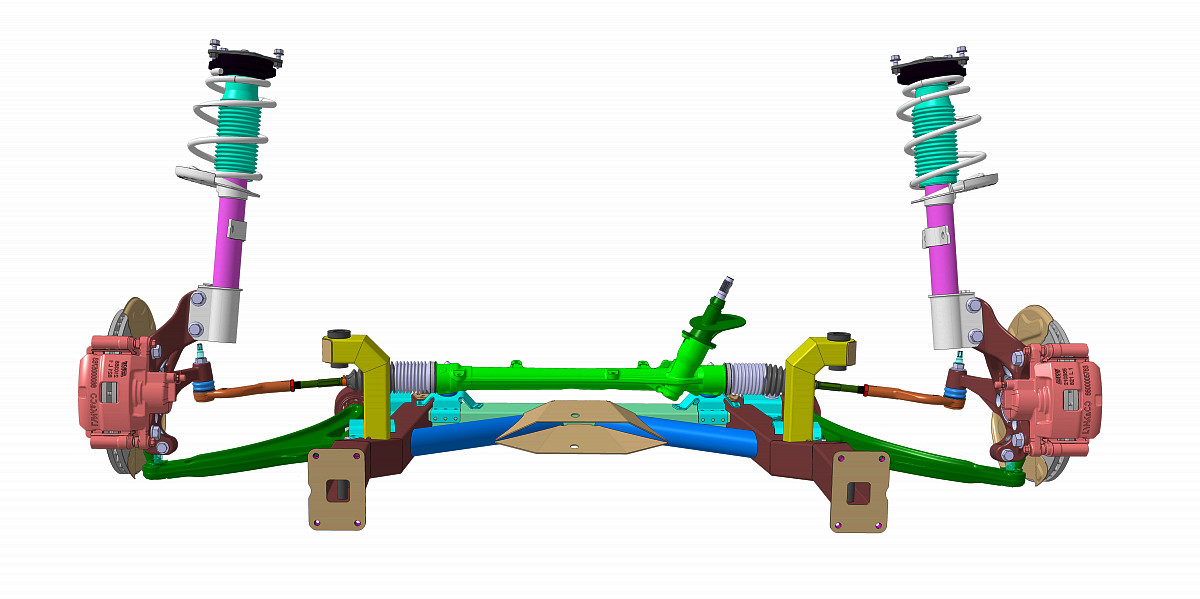
There will, of course, be differences from the production vehicle in terms of detail. The prototypes are safeguarded with predominantly quasistatic load cases. These parts will be further optimized in terms of component mass and service life ahead of final series production. The tools used to manufacture the series axles will also be different as, in contrast to the prototype manufacture, large quantities will be needed.
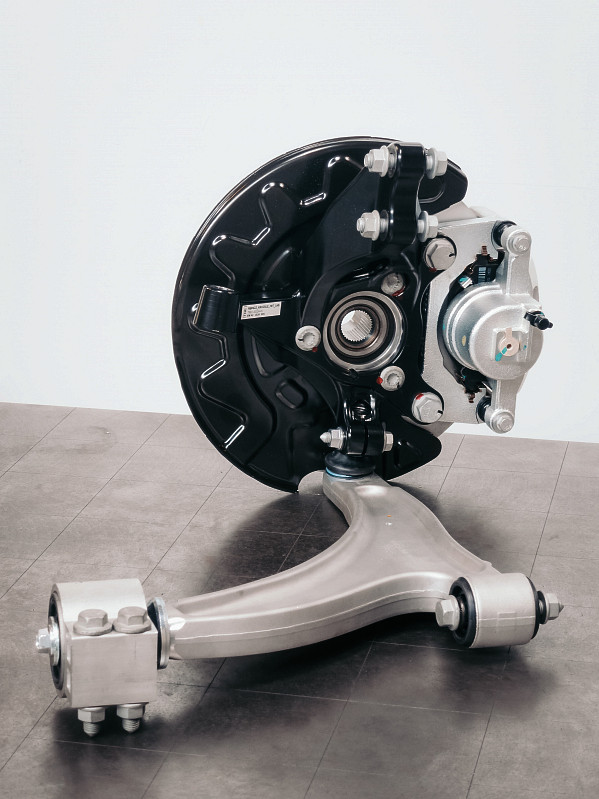
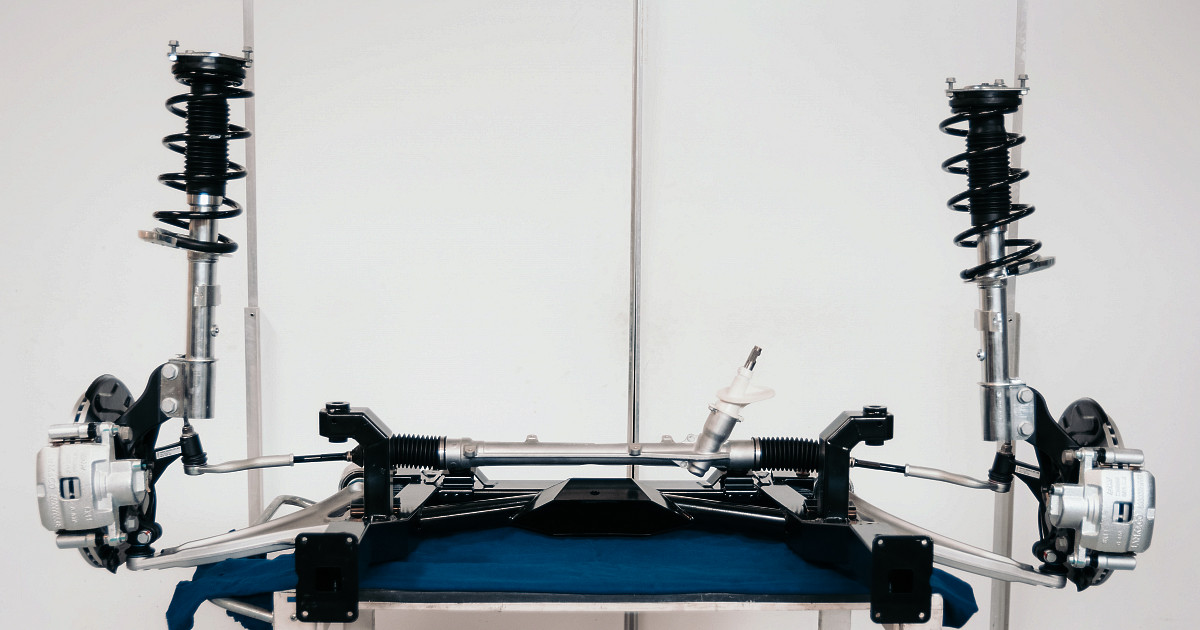
The ready-to-mount axle modules were shipped to Roding in October, where they have since been installed in the prototypes and tested for functionality. We have already shared a few photos of the manufacturing process in Roding with you. If you haven’t seen them yet,you can bring yourself up to speed here.
The Big Picture
TRE is a very important partner for us. We are thrilled to have the team’s expertise on our side. Furthermore, with Nico Rosberg, TRE shareholder and likewise a Formula One world champion, the team is also being backed by a sustainable entrepreneur and investor. Nico seemed very impressed by the Sion and Sono Motors, and shares our objective of advancing a positive change for society and the environment: “As a sustainability entrepreneur, it matters a great deal to me that we are applying our expertise to the development of the Sion by Sono Motors and are further developing the future of alternative mobility concepts.”
Regarding the project, we wholeheartedly agree with TRE CEO Eckardt Döhrer, who says: “We are delighted to be able to apply our sound expertise and TRE’s more than 20 years of experience in the area of chassis development to the development of the Sion with Sono Motors and, in the process, to be playing a part in shaping the technological progress made with future-oriented mobility concepts.” With partners like this, we can achieve our ambitious goals!